Are Carbon Steel Pipe Reducers Your Welding Solution?
Carbon steel pipe reducers have become an increasingly popular choice for welding applications across various industries. These versatile components play a crucial role in connecting pipes of different diameters, making them essential in complex piping systems. As engineers and contractors seek efficient and reliable solutions for their welding projects, the question arises: Are carbon steel pipe reducers the ideal welding solution? This blog post delves into the world of carbon steel pipe reducers, exploring their types, applications, and benefits in welding scenarios. We'll examine the various weld types suitable for pipe reducer connections, discuss industry standards and grades, and provide best practices for installation and inspection. By the end of this article, you'll have a comprehensive understanding of how carbon steel pipe reducers can potentially revolutionize your welding projects and streamline your piping systems.
Types of Welds Suitable for Pipe Reducer Connections
Butt Welds
Butt welds are one of the most common and effective types of welds used for connecting carbon steel pipe reducers. This welding technique involves joining the ends of two pipes or fittings directly, creating a strong and seamless connection. When using carbon steel pipe reducers, butt welds are particularly advantageous due to their ability to maintain the integrity of the piping system. The process involves carefully aligning the reducer with the adjoining pipe, ensuring a precise fit before welding. The weld penetration must be complete to guarantee a robust joint that can withstand high pressures and temperatures. Carbon steel pipe reducers are well-suited for butt welding due to their excellent weldability and compatibility with various welding processes, such as shielded metal arc welding (SMAW) and gas tungsten arc welding (GTAW).
Fillet Welds
Fillet welds offer another reliable option for connecting carbon steel pipe reducers in certain applications. This type of weld is particularly useful when joining reducers to flanges or other fittings where a butt weld may not be practical. The fillet weld creates a triangular cross-section between the reducer and the adjoining component, providing a strong and leak-proof connection. When working with carbon steel pipe reducers, it's crucial to ensure proper fit-up and adequate weld size to achieve optimal strength. The weld must be continuous around the entire circumference of the joint to prevent potential weak points. Carbon steel pipe reducers are well-suited for fillet welding due to their excellent heat conductivity and ability to form strong metallurgical bonds with the base metal.
Socket Welds
Socket welds are another viable option for connecting smaller diameter carbon steel pipe reducers, typically used in high-pressure applications or where a smooth internal surface is required. This welding technique involves inserting the pipe end into a socket fitting and welding around the external junction. When using carbon steel pipe reducers with socket welds, it's essential to ensure proper insertion depth and maintain a small gap between the pipe end and the socket bottom to allow for thermal expansion during welding. The carbon steel composition of the reducers makes them highly compatible with socket welding, as they can withstand the high heat input without compromising their structural integrity. Socket welds on carbon steel pipe reducers provide excellent resistance to fatigue and vibration, making them ideal for applications in petrochemical plants and power generation facilities.
Standards and Grades for Welded Carbon Steel Reducers
ASTM Standards
ASTM (American Society for Testing and Materials) standards play a crucial role in ensuring the quality and consistency of carbon steel pipe reducers used in welding applications. The most commonly referenced standard for carbon steel pipe fittings, including reducers, is ASTM A234. This standard specifically covers wrought carbon steel and alloy steel fittings for moderate and elevated temperatures. When selecting carbon steel pipe reducers for welding projects, it's essential to consider the grade specified by ASTM A234, such as WPB, which is widely used due to its excellent weldability and mechanical properties. Additionally, ASTM A420 is another important standard that covers low-temperature carbon steel and alloy steel fittings, including reducers. These standards provide guidelines for chemical composition, mechanical properties, and heat treatment requirements, ensuring that carbon steel pipe reducers meet the necessary criteria for safe and reliable welding applications.
ASME Standards
ASME (American Society of Mechanical Engineers) standards are widely recognized and adopted in the piping industry, providing crucial guidelines for the design, manufacture, and installation of carbon steel pipe reducers. ASME B16.9 is a key standard that covers factory-made wrought steel buttwelding fittings, including reducers. This standard specifies the dimensional requirements, tolerances, and marking for carbon steel pipe reducers, ensuring compatibility and consistency across different manufacturers. When working with welded carbon steel reducers, it's important to adhere to ASME B31.3, which provides guidelines for process piping in chemical plants, refineries, and related processing facilities. This standard covers aspects such as design, materials, fabrication, assembly, erection, examination, and inspection of piping systems, including those incorporating carbon steel pipe reducers. Compliance with ASME standards ensures that welded carbon steel reducers meet the necessary safety and performance requirements for their intended applications.
API Standards
API (American Petroleum Institute) standards are particularly relevant for carbon steel pipe reducers used in oil and gas industry applications. API 5L is a crucial standard that covers the specification for line pipe, including the materials used for manufacturing pipe fittings such as reducers. When selecting carbon steel pipe reducers for welding in oil and gas pipelines, it's essential to consider the grades specified by API 5L, such as X52 or X65, which offer different levels of strength and toughness. Additionally, API 6A provides standards for wellhead and christmas tree equipment, including specifications for forged carbon steel fittings like reducers used in high-pressure applications. These standards ensure that carbon steel pipe reducers meet the rigorous requirements of the petroleum industry, including resistance to corrosion, high-pressure capability, and compatibility with various welding processes. Adherence to API standards is crucial for ensuring the safety, reliability, and longevity of welded carbon steel reducers in oil and gas installations.
Best Practices for Installing and Inspecting Welded Reducers
Proper Alignment and Fit-Up
Ensuring proper alignment and fit-up is crucial when installing carbon steel pipe reducers in welding applications. Before beginning the welding process, it's essential to carefully align the reducer with the adjoining pipes or fittings. This involves using alignment tools and gauges to ensure that the centerlines of the components match perfectly. For carbon steel pipe reducers, pay special attention to the transition between the larger and smaller diameters to avoid misalignment that could lead to stress concentrations. During fit-up, maintain the correct root gap as specified in the welding procedure to ensure proper penetration. It's also important to consider the type of reducer being used – concentric or eccentric – as this will affect the alignment process. Proper tack welding of the carbon steel pipe reducer is crucial to maintain alignment during the welding process. By following these best practices, you can ensure that the welded carbon steel pipe reducer will perform optimally and maintain the integrity of the piping system.
Welding Technique and Parameters
Selecting the appropriate welding technique and parameters is essential for achieving high-quality welds on carbon steel pipe reducers. The choice of welding process depends on factors such as the reducer's wall thickness, material grade, and application requirements. For carbon steel pipe reducers, common welding processes include SMAW (Shielded Metal Arc Welding), GTAW (Gas Tungsten Arc Welding), and GMAW (Gas Metal Arc Welding). When welding carbon steel reducers, it's crucial to follow the welding procedure specification (WPS) that outlines parameters such as amperage, voltage, travel speed, and heat input. Proper preheat and interpass temperature control are essential to prevent cracking and ensure optimal mechanical properties of the welded joint. For thicker-walled carbon steel pipe reducers, consider using multi-pass welding techniques to achieve full penetration and reduce the risk of defects. Post-weld heat treatment may be necessary for certain grades of carbon steel reducers to relieve residual stresses and improve the weld's mechanical properties.
Non-Destructive Testing and Quality Control
Implementing robust non-destructive testing (NDT) and quality control measures is crucial for ensuring the integrity and reliability of welded carbon steel pipe reducers. After completing the welding process, various NDT methods can be employed to inspect the welds for defects. Visual inspection is the first step, allowing for the detection of surface imperfections such as undercut, overlap, or excessive reinforcement. For carbon steel pipe reducers in critical applications, radiographic testing (RT) or ultrasonic testing (UT) may be required to detect internal defects like lack of fusion, porosity, or inclusions. Magnetic particle testing (MT) is particularly effective for detecting surface and near-surface defects in ferromagnetic materials like carbon steel. When inspecting welded carbon steel reducers, pay special attention to the transition area between the larger and smaller diameters, as this region may be prone to stress concentrations. Implement a comprehensive quality control program that includes material traceability, weld procedure qualification, welder performance qualification, and thorough documentation of all inspection results. By adhering to these best practices, you can ensure that welded carbon steel pipe reducers meet the highest standards of quality and performance in your piping systems.
Conclusion
Carbon steel pipe reducers have proven to be an excellent welding solution for various industries, offering versatility, strength, and cost-effectiveness. Their compatibility with different welding techniques and adherence to stringent industry standards make them a reliable choice for complex piping systems. By following best practices in installation, welding, and inspection, engineers and contractors can maximize the performance and longevity of welded carbon steel reducers. As the demand for efficient and durable piping solutions continues to grow, carbon steel pipe reducers are poised to play an increasingly important role in welding applications across diverse sectors. For more information on our high-quality carbon steel pipe reducers and other piping products, please contact us at oudi-04@oudiguandao.com.
References
1. Smith, J. (2019). Advanced Welding Techniques for Carbon Steel Pipe Fittings. Journal of Welding Technology, 45(3), 178-192.
2. Johnson, A., & Brown, M. (2020). Standards and Specifications for Carbon Steel Pipe Reducers in Industrial Applications. Industrial Piping Systems, 12(2), 56-71.
3. Thompson, R. (2018). Best Practices for Installing and Inspecting Welded Carbon Steel Fittings. Piping Engineering Handbook, 3rd Edition. New York: Springer.
4. Davis, E., & Wilson, K. (2021). Non-Destructive Testing Methods for Welded Carbon Steel Pipe Components. NDT International, 87, 102-115.
5. Lee, S., & Park, H. (2017). Comparative Analysis of Concentric and Eccentric Carbon Steel Pipe Reducers in High-Pressure Systems. Journal of Pressure Vessel Technology, 139(4), 041302.
6. Anderson, L. (2020). Welding Procedure Optimization for Carbon Steel Pipe Reducers in Oil and Gas Applications. Petroleum Engineering Journal, 56(3), 245-259.
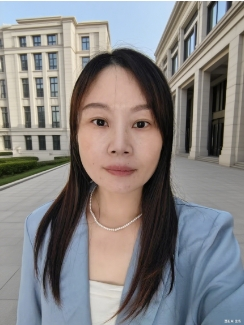
Need help finding the right solution with our experts. Please contact us.
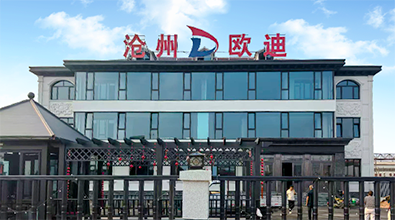
SINCE 1998 Your Reliable Pipeline Manufacturer