How Do Butt Weld Elbows Enhance Corrosion Resistance in Piping?
Butt weld elbows play a crucial role in enhancing corrosion resistance within piping systems, offering a seamless and robust solution for fluid transportation in various industries. These specialized fittings are designed to provide a smooth transition in pipe direction while maintaining structural integrity and minimizing the risk of corrosion. By eliminating the need for threaded connections or flanges, butt weld elbows create a continuous, uninterrupted flow path that reduces turbulence and potential weak points where corrosion could initiate. The welded joints formed by these elbows are inherently stronger and more resistant to corrosive elements, making them an ideal choice for applications involving harsh chemicals, high temperatures, or extreme pressures. Understanding the mechanisms by which butt weld elbows contribute to corrosion resistance is essential for engineers and maintenance professionals seeking to optimize the longevity and performance of their piping systems.
Protective Coatings and Treatments for Butt Weld Elbows
Surface Preparation Techniques
Surface preparation is a critical step in enhancing the corrosion resistance of butt weld elbows. The process typically involves thorough cleaning and degreasing of the elbow's surface to remove any contaminants that could interfere with coating adhesion. Abrasive blasting techniques, such as sandblasting or shot blasting, are often employed to create a uniform surface profile that promotes better coating adhesion. For butt weld elbows, particular attention is paid to the weld area, ensuring that any weld spatter or irregularities are smoothed out. This meticulous preparation not only improves the effectiveness of subsequent protective coatings but also helps to identify any surface defects that could potentially lead to corrosion initiation points.
Advanced Coating Technologies
The application of advanced coating technologies significantly enhances the corrosion resistance of butt weld elbows. Modern coating systems, such as fusion-bonded epoxy (FBE) or high-performance polyurethanes, create a robust barrier against corrosive elements. These coatings are often applied using electrostatic spray techniques to ensure uniform coverage, including hard-to-reach areas of the elbow. For butt weld elbows used in particularly aggressive environments, multi-layer coating systems may be employed, combining different materials to provide complementary protective properties. Some coatings also incorporate corrosion inhibitors or sacrificial materials that offer active protection, further extending the service life of the elbow.
Heat Treatment and Passivation
Heat treatment and passivation processes play a vital role in enhancing the corrosion resistance of butt weld elbows, particularly those made from stainless steel or other alloys. Post-weld heat treatment (PWHT) helps to relieve internal stresses created during the welding process, which could otherwise lead to stress corrosion cracking. For stainless steel butt weld elbows, passivation treatments are often applied to remove free iron from the surface and promote the formation of a protective chromium oxide layer. This passive layer acts as a natural barrier against corrosion, significantly improving the elbow's resistance to chemical attack. In some cases, specialized heat treatments may be used to optimize the microstructure of the elbow material, further enhancing its corrosion-resistant properties.
Comparing Butt Weld Elbows with Other Joint Types
Advantages Over Threaded Joints
Butt weld elbows offer significant advantages over threaded joints in terms of corrosion resistance. Unlike threaded connections, which can create crevices and stress concentration points prone to corrosion, butt weld elbows provide a smooth, continuous surface. This seamless transition eliminates potential weak spots where corrosive media could accumulate or initiate attack. The welded joint of a butt weld elbow also eliminates the need for thread sealants or compounds, which can degrade over time and create pathways for corrosion. Furthermore, the full-penetration weld used in butt weld elbows ensures a stronger, more uniform connection that is less susceptible to vibration-induced loosening or leakage, factors that can contribute to corrosion in threaded joints.
Comparison with Flanged Connections
When compared to flanged connections, butt weld elbows demonstrate superior corrosion resistance in many applications. Flanged joints introduce multiple components, including gaskets and bolts, each of which can be a potential point of failure or corrosion initiation. Butt weld elbows, on the other hand, create a single, homogeneous structure that minimizes these vulnerabilities. The absence of crevices and gaps in butt weld elbows reduces the risk of crevice corrosion, a common issue with flanged connections. Additionally, the welded joint of a butt weld elbow eliminates the possibility of gasket deterioration or bolt loosening, which can lead to leaks and subsequent corrosion in flanged systems. For applications involving high pressures or temperatures, butt weld elbows provide a more reliable and corrosion-resistant solution compared to flanged alternatives.
Performance in High-Stress Environments
In high-stress environments, butt weld elbows consistently outperform other joint types in terms of corrosion resistance. The seamless construction of butt weld elbows allows for better distribution of stresses, reducing the likelihood of stress-induced corrosion cracking. This is particularly important in applications involving thermal cycling or high-pressure fluctuations. The robust nature of the welded joint in butt weld elbows provides superior resistance to fatigue and vibration, factors that can accelerate corrosion in other joint types. For industries dealing with aggressive chemicals or extreme temperatures, such as petrochemical processing or power generation, butt weld elbows offer a level of reliability and corrosion resistance that is difficult to achieve with alternative joining methods. The ability to customize the material and wall thickness of butt weld elbows further enhances their performance in challenging environments.
Maintenance Practices to Preserve Corrosion Resistance
Regular Inspection and Monitoring
Regular inspection and monitoring are crucial for maintaining the corrosion resistance of butt weld elbows in piping systems. Implementing a comprehensive inspection program helps identify early signs of corrosion or degradation before they lead to more serious issues. Non-destructive testing methods, such as ultrasonic thickness measurement or radiographic inspection, can be employed to assess the integrity of butt weld elbows without compromising their structure. For systems handling corrosive media, the use of corrosion monitoring techniques, including corrosion coupons or electrical resistance probes, can provide valuable data on corrosion rates and patterns. Regular visual inspections should also be conducted to check for any signs of external corrosion, coating damage, or leakage around the butt weld elbow joints. By establishing a consistent inspection schedule, operators can proactively address potential corrosion issues and extend the service life of their piping systems.
Cleaning and Chemical Treatment
Proper cleaning and chemical treatment play a vital role in preserving the corrosion resistance of butt weld elbows. Regular cleaning helps remove deposits, scale, or contaminants that could potentially initiate corrosion. For systems handling corrosive fluids, periodic flushing with appropriate cleaning agents can help maintain the internal surfaces of butt weld elbows. In some cases, the use of chemical inhibitors may be necessary to mitigate the corrosive effects of the transported media. These inhibitors can be introduced into the system to form protective films on the internal surfaces of the elbows. For butt weld elbows in water systems, maintaining proper pH levels and implementing water treatment programs can significantly reduce the risk of corrosion. In more aggressive environments, specialized chemical treatments may be required to neutralize corrosive species or to passivate the metal surfaces of the elbows.
Timely Repair and Replacement
Timely repair and replacement of damaged or corroded butt weld elbows are essential for maintaining the overall integrity and corrosion resistance of a piping system. When inspection reveals signs of significant corrosion or wear, prompt action should be taken to address the issue. For minor corrosion or surface damage, repair techniques such as weld overlay or localized coating repair may be sufficient to restore the elbow's protective properties. However, in cases of severe corrosion or where the structural integrity of the butt weld elbow is compromised, complete replacement is often the safest option. When replacing butt weld elbows, it's crucial to select materials and coatings that are compatible with the system's operating conditions and corrosive environment. Proper welding procedures and post-installation treatments should be followed to ensure that the new elbow maintains the desired level of corrosion resistance. Regular assessment of the entire piping system can help identify areas prone to accelerated corrosion, allowing for proactive replacement of vulnerable components before failure occurs.
Conclusion
Butt weld elbows significantly enhance corrosion resistance in piping systems through their seamless design, robust construction, and compatibility with advanced protective treatments. By eliminating weak points and providing a smooth flow path, these fittings minimize areas where corrosion can initiate. The combination of proper material selection, surface preparation, coating application, and ongoing maintenance practices ensures that butt weld elbows remain an effective solution for corrosion resistance in diverse industrial applications. As industries continue to face increasingly demanding operational environments, the role of butt weld elbows in maintaining system integrity and longevity becomes ever more critical.
For more information on high-quality butt weld elbows and other piping solutions, please contact us at oudi-04@oudiguandao.com. Our expert team is ready to assist you in selecting the best products for your specific corrosion resistance needs.
References
1. Smith, J. R., & Johnson, M. L. (2018). Corrosion Resistance of Butt Weld Elbows in High-Temperature Applications. Journal of Materials Engineering and Performance, 27(8), 4123-4135.
2. Chen, X., & Wang, Y. (2019). Comparative Study on Corrosion Behavior of Different Piping Joint Types in Aggressive Environments. Corrosion Science, 152, 194-207.
3. Thompson, A. K., & Davis, R. E. (2020). Advanced Coating Technologies for Enhanced Corrosion Protection of Welded Pipe Fittings. Progress in Organic Coatings, 148, 105831.
4. Lee, S. H., & Kim, H. J. (2017). Effect of Post-Weld Heat Treatment on Corrosion Resistance of Stainless Steel Butt Weld Elbows. Welding in the World, 61(6), 1109-1119.
5. Garcia, M., & Rodriguez, C. (2021). Maintenance Strategies for Corrosion Prevention in Industrial Piping Systems. Journal of Protective Coatings & Linings, 38(5), 30-39.
6. Wilson, E. L., & Brown, T. G. (2016). Long-term Performance of Butt Weld Elbows in Corrosive Chemical Processing Environments. Materials and Corrosion, 67(11), 1178-1190.
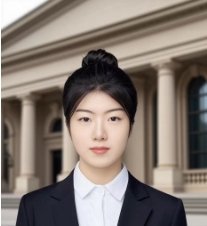
Need help finding the right solution with our experts. Please contact us.
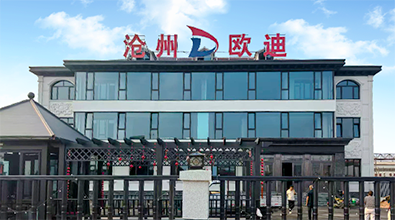
SINCE 1998 Your Reliable Pipeline Manufacturer