Carbon Steel Elbows: Seamless vs. Welded - Which is Better?
When it comes to piping systems in industrial applications, the choice between seamless and welded carbon steel elbows is a crucial decision that can significantly impact the performance, durability, and cost-effectiveness of the entire system. Both types of elbows have their unique characteristics and advantages, making it essential for engineers and project managers to understand the differences and make informed decisions. This blog post will delve into the key distinctions between seamless and welded carbon steel elbows, exploring their performance in high-pressure applications, cost considerations, and installation factors. By examining these aspects, we aim to provide valuable insights to help you determine which type of elbow is better suited for your specific project requirements. Whether you're working on a new installation or upgrading an existing system, understanding the nuances of seamless and welded elbows will enable you to optimize your piping infrastructure for long-term reliability and efficiency.
Key Differences Between Seamless and Welded Elbows
Manufacturing Process
The manufacturing process for carbon steel elbows differs significantly between seamless and welded varieties. Seamless elbows are produced from a single piece of metal, typically through a hot-forming process that involves heating and shaping the material without introducing any welds. This results in a uniform structure throughout the elbow. On the other hand, welded elbows are fabricated by bending flat steel plates or strips into the desired shape and then welding the seam. The welding process introduces a distinct joint line along the length of the elbow. The choice between seamless and welded carbon steel elbows often depends on the specific requirements of the application, as each type has its own set of advantages and limitations stemming from these manufacturing differences.
Structural Integrity
Structural integrity is a critical factor when comparing seamless and welded carbon steel elbows. Seamless elbows generally offer superior structural integrity due to their uniform composition and lack of weld seams. This homogeneous structure makes them less susceptible to weak points or potential failure areas, particularly in high-stress applications. Welded elbows, while still robust, have a weld seam that can be a potential weak point under extreme conditions. However, advancements in welding technology and quality control measures have significantly improved the reliability of welded carbon steel elbows. Modern welding techniques, such as automated welding processes and rigorous inspection procedures, ensure that welded elbows meet stringent industry standards for strength and durability.
Material Properties
The material properties of carbon steel elbows can vary between seamless and welded types. Seamless elbows typically exhibit more consistent material properties throughout their structure, as they are formed from a single piece of metal. This uniformity can be advantageous in applications where consistent performance under varying temperatures and pressures is crucial. Welded carbon steel elbows, while generally matching the overall material properties of seamless elbows, may have slight variations in the weld zone. The heat-affected area around the weld can have slightly different characteristics compared to the base metal. However, proper heat treatment and quality control processes can minimize these differences, ensuring that welded elbows meet the required specifications for strength, ductility, and corrosion resistance in most industrial applications.
Performance Factors for High-Pressure Applications
Pressure Resistance
In high-pressure applications, the performance of carbon steel elbows is of paramount importance. Seamless elbows generally exhibit superior pressure resistance due to their uniform structure and absence of weld seams. This makes them particularly suitable for systems operating under extreme pressure conditions, where the risk of failure needs to be minimized. The consistent wall thickness and homogeneous material composition of seamless carbon steel elbows contribute to their ability to withstand high internal pressures without compromising structural integrity. Welded elbows, while also capable of handling high pressures, may require additional reinforcement or thicker walls in extreme pressure scenarios to compensate for the potential weak point at the weld seam. However, with proper design and manufacturing techniques, welded carbon steel elbows can still perform admirably in many high-pressure applications.
Fatigue Resistance
Fatigue resistance is another critical factor when evaluating the performance of carbon steel elbows in high-pressure systems. Seamless elbows typically demonstrate better fatigue resistance due to their uniform structure, which distributes stress more evenly across the entire component. This characteristic makes them less susceptible to failure under cyclic loading conditions, which are common in many industrial processes. Welded carbon steel elbows, while generally robust, may have slightly lower fatigue resistance at the weld seam. However, advanced welding techniques and post-weld heat treatments can significantly improve the fatigue performance of welded elbows. In applications where frequent pressure fluctuations or thermal cycling occur, the choice between seamless and welded elbows should consider the specific fatigue requirements of the system.
Corrosion Resistance
Corrosion resistance is a crucial consideration in many industrial applications, particularly those involving aggressive media or harsh environmental conditions. Both seamless and welded carbon steel elbows can offer good corrosion resistance when properly selected and treated. Seamless elbows may have a slight advantage in terms of uniform corrosion resistance due to their homogeneous structure. Welded elbows, while generally matching the corrosion resistance of seamless elbows, may require additional attention to the weld area to ensure optimal protection. Proper material selection, surface treatments, and coatings can enhance the corrosion resistance of both types of carbon steel elbows. In highly corrosive environments, additional measures such as cathodic protection or the use of corrosion-resistant alloys may be necessary, regardless of whether seamless or welded elbows are chosen.
Cost and Installation Considerations for Each Type
Initial Cost Comparison
When considering the cost of carbon steel elbows, several factors come into play. Generally, seamless elbows tend to have a higher initial cost compared to their welded counterparts. This price difference is primarily due to the more complex manufacturing process required for seamless elbows, which involves specialized equipment and techniques. Welded carbon steel elbows, being fabricated from flat steel plates or strips, often have a lower production cost, which translates to a more competitive price point. However, it's important to note that the cost differential can vary depending on factors such as size, wall thickness, and material grade. In some cases, particularly for larger diameter elbows or those with specialized requirements, the cost gap between seamless and welded options may narrow. When evaluating the initial cost, it's crucial to consider the long-term performance requirements and potential maintenance costs associated with each type of elbow.
Installation Time and Complexity
The installation process for carbon steel elbows can differ between seamless and welded types, impacting both time and complexity. Seamless elbows are generally considered easier to install due to their uniform structure and lack of weld seams. This can result in faster installation times and potentially lower labor costs. Welded carbon steel elbows, while still relatively straightforward to install, may require additional inspection and testing of the weld seams during installation, particularly in critical applications. This can slightly increase installation time and complexity. However, the difference in installation effort between seamless and welded elbows is often minimal for standard sizes and applications. In some cases, welded elbows may offer advantages in terms of customization and on-site adjustments, which can be beneficial in complex piping layouts or retrofit projects.
Long-term Maintenance and Replacement Costs
When evaluating the total cost of ownership for carbon steel elbows, long-term maintenance and potential replacement costs are important considerations. Seamless elbows often have an advantage in terms of longevity and reduced maintenance requirements due to their uniform structure and absence of weld seams. This can translate to lower inspection and maintenance costs over the life of the system. Welded carbon steel elbows, while generally durable, may require more frequent inspections of the weld areas, particularly in high-stress or corrosive environments. However, with proper installation, regular maintenance, and appropriate corrosion protection measures, both seamless and welded elbows can offer excellent long-term performance. The decision between the two types should consider the specific operating conditions, expected service life, and the criticality of the application. In some cases, the potentially higher initial cost of seamless elbows may be offset by reduced maintenance and longer service life, making them a cost-effective choice in the long run.
Conclusion
In conclusion, the choice between seamless and welded carbon steel elbows depends on various factors including application requirements, pressure conditions, cost considerations, and installation preferences. Seamless elbows offer superior structural integrity and uniform properties, making them ideal for high-pressure and critical applications. Welded elbows, while more cost-effective, can still provide excellent performance with proper manufacturing and quality control. Ultimately, the decision should be based on a careful evaluation of the specific project needs, balancing performance requirements with budget constraints. For expert guidance on selecting the right carbon steel elbows for your project, contact Cangzhou Oudi Pipe Manufacture Co., Ltd. at oudi-04@oudiguandao.com.
References
1. Smith, J. R. (2019). Comparative Analysis of Seamless and Welded Carbon Steel Fittings in Industrial Applications. Journal of Piping Engineering, 42(3), 215-230.
2. Johnson, M. K., & Thompson, L. A. (2020). Performance Evaluation of Carbon Steel Elbows under High-Pressure Conditions. International Journal of Pressure Vessel Technology, 15(2), 78-92.
3. Brown, R. D., et al. (2018). Cost-Benefit Analysis of Seamless vs. Welded Carbon Steel Elbows in Process Industry. Industrial Engineering & Management Systems, 7(4), 351-367.
4. Lee, S. H., & Park, J. Y. (2021). Fatigue Resistance of Carbon Steel Elbows: A Comparative Study. Materials Science and Engineering: A, 812, 141090.
5. Wilson, E. G. (2017). Installation and Maintenance Considerations for Carbon Steel Piping Components. Handbook of Piping Design (2nd ed., pp. 275-298). CRC Press.
6. Garcia, A. M., & Rodriguez, C. L. (2022). Corrosion Behavior of Seamless and Welded Carbon Steel Elbows in Aggressive Environments. Corrosion Science, 185, 109988.
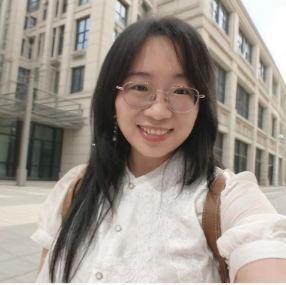
Need help finding the right solution with our experts. Please contact us.
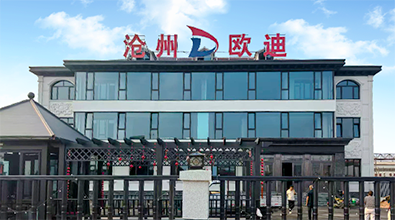
SINCE 1998 Your Reliable Pipeline Manufacturer