Why Are Butt Weld Elbows Essential for Pipe Fitting Connections?
Butt weld elbows play a crucial role in the world of pipe fitting connections, serving as indispensable components in various industrial piping systems. These specialized fittings are designed to facilitate smooth directional changes in pipelines while maintaining structural integrity and flow efficiency. As industries continue to evolve and demand higher standards of safety, reliability, and performance, the importance of butt weld elbows has become increasingly apparent. Their ability to create seamless, robust connections makes them essential for applications ranging from oil and gas pipelines to chemical processing plants and power generation facilities. In this blog post, we will explore the key advantages of butt weld elbows, their role in ensuring leak-free connections, and the common materials and standards used in their manufacture. By understanding the significance of these fittings, we can appreciate their vital contribution to the efficiency and safety of modern industrial piping systems.
Key Advantages of Using Butt Weld Elbows in Piping Systems
Enhanced Structural Integrity
Butt weld elbows offer superior structural integrity compared to other types of pipe fittings. The seamless connection created by the welding process ensures a uniform distribution of stress along the joint, reducing the risk of weak points or potential failure areas. This enhanced strength is particularly crucial in high-pressure or high-temperature applications where the piping system is subjected to significant mechanical and thermal stresses. The use of butt weld elbows allows for a more robust and durable piping network, capable of withstanding the demanding conditions often encountered in industrial environments. Furthermore, the smooth internal surface of butt weld elbows minimizes turbulence and pressure drop, contributing to the overall efficiency of the fluid flow within the system.
Improved Flow Characteristics
One of the key advantages of butt weld elbows is their ability to maintain smooth flow characteristics within the piping system. The seamless transition provided by these fittings allows for optimal fluid dynamics, reducing turbulence and minimizing pressure losses. This is particularly important in applications where maintaining consistent flow rates and pressure is critical, such as in the transportation of liquids or gases in industrial processes. The design of butt weld elbows, with their gradual curve and uniform internal diameter, ensures that the fluid or gas passing through experiences minimal disruption. This not only enhances the overall efficiency of the system but also reduces the risk of erosion and wear on the piping components, ultimately extending the lifespan of the entire piping network.
Cost-Effective Long-Term Solution
While the initial cost of butt weld elbows may be higher compared to some alternative fittings, they prove to be a cost-effective long-term solution for piping systems. The durability and reliability of butt weld elbows result in reduced maintenance requirements and fewer replacements over the lifetime of the piping system. This translates to lower operational costs and minimized downtime for repairs or replacements. Additionally, the superior performance of butt weld elbows in terms of flow efficiency can lead to energy savings in pumping or compression systems. The seamless nature of the connection also reduces the risk of leaks, which can be costly both in terms of lost product and potential environmental damage. When considering the total cost of ownership, butt weld elbows often emerge as the most economical choice for industrial piping applications.
How Butt Weld Elbows Ensure Leak-Free Connections?
Precision Welding Techniques
The key to ensuring leak-free connections with butt weld elbows lies in the precision welding techniques employed during installation. Skilled welders use advanced methods such as TIG (Tungsten Inert Gas) or MIG (Metal Inert Gas) welding to create a seamless fusion between the elbow and the adjoining pipes. This process involves carefully aligning the components, preheating the materials to the appropriate temperature, and executing the weld with meticulous attention to detail. The result is a joint that is as strong as, if not stronger than, the base material of the pipes and elbows. The welding process also allows for complete penetration of the joint, eliminating any potential gaps or voids that could lead to leaks. This level of precision ensures that butt weld elbows provide a reliable, leak-free connection that can withstand the pressures and stresses of industrial piping systems.
Material Compatibility and Preparation
Ensuring leak-free connections with butt weld elbows also depends on proper material compatibility and preparation. The materials of the elbow and the connecting pipes must be carefully matched to ensure optimal welding results and long-term performance. Prior to welding, the surfaces of both the elbow and the pipe ends are meticulously cleaned and prepared to remove any contaminants, oxides, or impurities that could compromise the integrity of the weld. This preparation often involves grinding, wire brushing, or chemical cleaning to achieve a pristine surface. Additionally, the pipe ends are beveled to create the appropriate weld groove, facilitating full penetration of the weld and ensuring a strong, leak-free joint. The attention to material compatibility and preparation is crucial in creating a homogeneous weld that can withstand the various stresses and pressures encountered in industrial piping systems.
Quality Control and Testing
The final step in ensuring leak-free connections with butt weld elbows involves rigorous quality control measures and comprehensive testing procedures. After the welding process is complete, the joints are subjected to various non-destructive testing methods such as radiographic testing, ultrasonic testing, or dye penetrant inspection to detect any potential flaws or defects in the weld. These tests can identify issues such as porosity, lack of fusion, or cracks that could compromise the integrity of the connection. In addition to these inspections, pressure testing is often performed on the entire piping system to verify its leak-free status under operating conditions. This may involve hydrostatic testing, where the system is filled with water and pressurized to a level above its normal operating pressure, or pneumatic testing using compressed air or inert gas. These quality control measures and testing procedures provide confidence in the leak-free performance of butt weld elbow connections in critical industrial applications.
Common Materials and Standards for Butt Weld Elbows
Carbon Steel and Stainless Steel Options
Carbon steel and stainless steel are among the most commonly used materials for butt weld elbows, each offering distinct advantages for different applications. Carbon steel butt weld elbows, typically manufactured to standards such as ASTM A234 WPB, are widely used in general industrial piping systems due to their excellent strength, durability, and cost-effectiveness. They are particularly suitable for applications involving non-corrosive fluids and moderate temperatures. Stainless steel butt weld elbows, on the other hand, are preferred in applications where corrosion resistance is paramount. Grades such as 304L and 316L are commonly used, offering superior resistance to a wide range of corrosive media and high-temperature environments. The choice between carbon steel and stainless steel butt weld elbows depends on factors such as the nature of the fluid being transported, operating temperatures and pressures, and the corrosiveness of the environment.
Alloy Steel and Special Materials
For more demanding applications, alloy steel and special materials are used in the manufacture of butt weld elbows. Alloy steel elbows, such as those made from chrome-moly steels (e.g., ASTM A234 WP11, WP22), are employed in high-temperature services where creep resistance is crucial. These materials maintain their strength and structural integrity at elevated temperatures, making them ideal for power generation and petrochemical applications. In extremely corrosive environments or where contamination must be minimized, special materials like duplex stainless steels, nickel alloys (e.g., Inconel, Hastelloy), or titanium may be used for butt weld elbows. These materials offer exceptional resistance to specific types of corrosion or provide unique properties required for critical processes. The selection of alloy steel or special materials for butt weld elbows is often driven by the need to meet specific performance requirements in challenging industrial environments.
International Standards and Specifications
Butt weld elbows are manufactured and tested according to various international standards and specifications to ensure consistency, quality, and interchangeability across different applications and regions. Some of the most widely recognized standards include ASME B16.9, which covers factory-made wrought steel butt-welding fittings, and ASTM A234, which specifies the requirements for piping fittings of wrought carbon steel and alloy steel. Other important standards include EN 10253 for European applications and JIS B2311 for Japanese industrial standards. These specifications define critical aspects such as dimensions, tolerances, material composition, heat treatment requirements, and testing procedures. Compliance with these international standards ensures that butt weld elbows meet the rigorous demands of industrial piping systems and can be reliably integrated into global projects. Manufacturers often provide documentation certifying compliance with the relevant standards, giving engineers and end-users confidence in the performance and reliability of the fittings.
Conclusion
Butt weld elbows are indispensable components in modern piping systems, offering superior structural integrity, improved flow characteristics, and long-term cost-effectiveness. Their ability to create leak-free connections through precision welding techniques, proper material selection, and rigorous quality control makes them essential for a wide range of industrial applications. As industries continue to evolve and face new challenges, the importance of reliable and efficient piping solutions cannot be overstated. By understanding the advantages and applications of butt weld elbows, engineers and project managers can make informed decisions to ensure the safety, efficiency, and longevity of their piping systems. For more information on high-quality butt weld elbows and other pipe fittings, please contact us at oudi-04@oudiguandao.com.
References
1. Smith, J. A. (2018). Advanced Piping Design: Principles and Applications. Industrial Press.
2. Johnson, R. B., & Williams, S. T. (2019). Handbook of Piping Engineering and Construction. McGraw-Hill Education.
3. Chen, X., & Liu, Y. (2020). Welding Metallurgy of Stainless Steels. Springer International Publishing.
4. Thompson, M. K. (2017). Pipe Fitting and Piping Handbook. Butterworth-Heinemann.
5. Davis, J. R. (2021). Corrosion of Weldments. ASM International.
6. Anderson, P. L. (2019). Fracture Mechanics: Fundamentals and Applications. CRC Press.
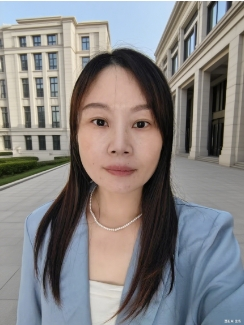
Need help finding the right solution with our experts. Please contact us.
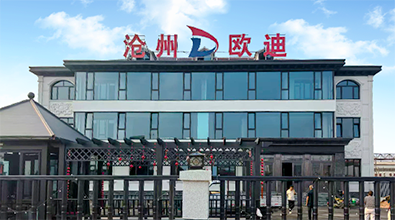
SINCE 1998 Your Reliable Pipeline Manufacturer