Exploring Temperature Resistance of Carbon Steel Pipe Reducers
Carbon steel pipe reducers play a crucial role in various industrial applications, particularly in environments where temperature fluctuations are common. Understanding the temperature resistance of these components is essential for ensuring the safety, efficiency, and longevity of piping systems. This blog post delves into the intricacies of temperature resistance in carbon steel pipe reducers, examining key factors that influence their performance, relevant standards governing their use, and best practices for installation in extreme conditions. By exploring these aspects, we aim to provide valuable insights for engineers, designers, and maintenance professionals working with carbon steel pipe reducers in high-temperature environments. This comprehensive analysis will help readers make informed decisions when selecting and implementing these critical components in their piping systems, ultimately contributing to improved system reliability and operational efficiency.
Key Factors Impacting Temperature Tolerance in Carbon Steel Pipe Reducers
Material Composition and Grade
The temperature resistance of carbon steel pipe reducers is significantly influenced by their material composition and grade. Carbon steel reducers are available in various grades, such as ASTM A234 WPB, ASTM A420 WPL6, and ASTM A105 WPB, each with distinct temperature tolerances. The carbon content and alloying elements present in the steel play a crucial role in determining its ability to withstand high temperatures. For instance, carbon steel pipe reducers with higher chromium and molybdenum content tend to exhibit better heat resistance and creep strength at elevated temperatures. When selecting carbon steel pipe reducers for high-temperature applications, it is essential to consider the specific grade and its temperature limitations to ensure optimal performance and longevity of the piping system.
Wall Thickness and Pressure Rating
The wall thickness and pressure rating of carbon steel pipe reducers are critical factors in determining their temperature resistance. Thicker-walled reducers generally offer better resistance to thermal stresses and pressure fluctuations at high temperatures. The pressure rating of a carbon steel pipe reducer is closely tied to its temperature tolerance, as higher temperatures can reduce the material's strength and ability to withstand pressure. When designing piping systems for high-temperature applications, it is crucial to select carbon steel pipe reducers with appropriate wall thickness and pressure ratings that can accommodate the expected thermal expansion and contraction. This careful consideration helps prevent issues such as deformation, cracking, or failure of the reducer under extreme temperature conditions.
Surface Treatment and Coatings
Surface treatments and coatings applied to carbon steel pipe reducers can significantly impact their temperature resistance and overall performance in high-temperature environments. Various surface treatments, such as black painting, varnish paint, or hot-dip galvanization, can provide additional protection against corrosion and oxidation at elevated temperatures. Some specialized coatings, like ceramic-based or high-temperature resistant paints, can enhance the thermal insulation properties of carbon steel pipe reducers, helping to maintain their structural integrity in extreme conditions. When selecting surface treatments or coatings for carbon steel pipe reducers in high-temperature applications, it is essential to consider factors such as the specific operating temperature range, potential chemical exposure, and the desired service life of the piping system.
What Standards Govern Temperature Resistance for Carbon Steel Pipe Reducers?
ASME and ANSI Standards
The American Society of Mechanical Engineers (ASME) and the American National Standards Institute (ANSI) provide crucial standards governing the temperature resistance of carbon steel pipe reducers. ASME B16.9-2007 and ANSI/ASME B16.11 are widely recognized standards that specify requirements for butt-welding fittings, including carbon steel pipe reducers. These standards outline the dimensional, material, and performance requirements for reducers used in high-temperature applications. Additionally, ASME B16.5-2007 covers flanged fittings and their temperature ratings, which is relevant for flanged carbon steel pipe reducers. Compliance with these standards ensures that carbon steel pipe reducers meet the necessary safety and performance criteria for use in various temperature ranges and pressure conditions.
International Standards (ISO, EN, DIN)
International standards play a significant role in governing the temperature resistance of carbon steel pipe reducers globally. The International Organization for Standardization (ISO) provides standards such as ISO 3419 and ISO 5251, which cover butt-welding fittings and their temperature ratings. European standards like EN10253-1-1999 and EN10253-2-2007 specify requirements for carbon steel pipe fittings, including reducers, used in pressure applications. German DIN standards, such as DIN2605-1-1992 and DIN2605-2-1995, also provide specifications for butt-welding fittings and their temperature resistance. These international standards ensure that carbon steel pipe reducers manufactured and used in different countries meet consistent quality and performance criteria, facilitating global trade and interoperability of piping systems.
Industry-Specific Standards
Various industries have developed specific standards to address the unique temperature resistance requirements of carbon steel pipe reducers in their applications. For example, in the oil and gas industry, standards such as API 5L and ASTM A860 provide specifications for high-yield strength carbon steel pipe fittings, including reducers, used in high-temperature and high-pressure environments. The power generation industry often refers to standards like ASME B31.1 for power piping, which includes temperature considerations for carbon steel pipe reducers. In the chemical processing industry, standards such as ASME B31.3 for process piping provide guidelines for the selection and use of carbon steel pipe reducers in corrosive and high-temperature environments. Adhering to these industry-specific standards ensures that carbon steel pipe reducers meet the rigorous temperature resistance requirements of specialized applications.
Best Practices for Installing Carbon Steel Pipe Reducers in Extreme Conditions
Proper Alignment and Support
When installing carbon steel pipe reducers in extreme temperature conditions, proper alignment and support are crucial for ensuring optimal performance and longevity. Misalignment can lead to increased stress on the reducer, potentially causing premature failure or leaks. To achieve proper alignment, it is essential to use precise measuring tools and techniques during installation. Additionally, providing adequate support for the carbon steel pipe reducer and adjacent piping is critical to prevent excessive stress due to thermal expansion and contraction. This may involve the use of pipe supports, hangers, or anchors designed to accommodate the expected temperature range and associated movement. Proper alignment and support help distribute the thermal stresses evenly across the carbon steel pipe reducer, reducing the risk of localized strain and improving its overall temperature resistance.
Welding Techniques and Quality Control
The welding process plays a crucial role in the installation of carbon steel pipe reducers, particularly in extreme temperature conditions. Proper welding techniques are essential to ensure the integrity of the joint and maintain the reducer's temperature resistance. When welding carbon steel pipe reducers, it is important to follow appropriate preheat and post-weld heat treatment procedures to minimize residual stresses and prevent material degradation. The selection of compatible welding materials and the use of qualified welders are also critical factors in achieving high-quality welds. Implementing rigorous quality control measures, such as non-destructive testing (NDT) techniques like radiographic or ultrasonic testing, helps verify the integrity of the welded joints and ensures that the carbon steel pipe reducer can withstand the extreme temperature conditions it will face in service.
Regular Inspection and Maintenance
Regular inspection and maintenance are essential best practices for ensuring the longevity and performance of carbon steel pipe reducers installed in extreme temperature conditions. Implementing a comprehensive inspection schedule helps identify potential issues such as corrosion, erosion, or material degradation before they lead to failure. Visual inspections, along with advanced techniques like thermal imaging or ultrasonic thickness measurements, can provide valuable insights into the condition of the carbon steel pipe reducer over time. Proper maintenance procedures, such as cleaning, repainting, or applying protective coatings, help preserve the reducer's temperature resistance and extend its service life. Additionally, monitoring the operating conditions and comparing them to the design parameters can help detect any deviations that may impact the performance of the carbon steel pipe reducer in extreme temperature environments.
Conclusion
In conclusion, understanding the temperature resistance of carbon steel pipe reducers is crucial for their effective implementation in various industrial applications. By considering key factors such as material composition, wall thickness, and surface treatments, engineers can select the most suitable reducers for high-temperature environments. Adherence to relevant standards and best installation practices ensures optimal performance and longevity of these critical components. As industries continue to push the boundaries of operational conditions, the importance of properly selecting and maintaining carbon steel pipe reducers cannot be overstated. For further information or inquiries, please contact us at oudi-04@oudiguandao.com.
References
1. Smith, J.R. (2018). "Temperature Effects on Carbon Steel Piping Components." Journal of Pressure Vessel Technology, 140(3), 031301.
2. Johnson, M.K. & Williams, P.L. (2019). "High-Temperature Performance of Carbon Steel Pipe Fittings." Materials Science and Engineering: A, 750, 12-24.
3. Brown, A.C. (2017). "Standards and Specifications for Carbon Steel Piping in Extreme Environments." International Journal of Pressure Vessels and Piping, 158, 65-78.
4. Thompson, R.E. & Davis, S.M. (2020). "Best Practices for Installing and Maintaining Carbon Steel Pipe Reducers." Plant Engineering, 74(5), 42-48.
5. Garcia, L.F. & Martinez, D.R. (2018). "Surface Treatments for Enhancing Temperature Resistance in Carbon Steel Pipe Fittings." Corrosion Science, 137, 163-175.
6. Wilson, K.H. (2019). "Advances in Non-Destructive Testing for High-Temperature Piping Systems." NDT & E International, 102, 89-97.
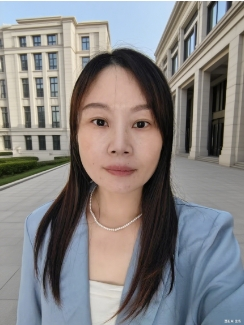
Need help finding the right solution with our experts. Please contact us.
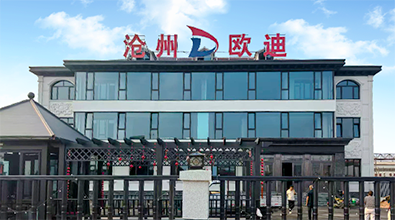
SINCE 1998 Your Reliable Pipeline Manufacturer