Space-Saving Solutions: Long Radius Elbows in Industrial Piping
In the realm of industrial piping systems, optimizing space utilization while maintaining efficiency is a constant challenge. As industries evolve and facilities become more complex, the need for innovative solutions to maximize available space has never been more critical. Enter long radius elbows – a game-changing component in industrial piping that offers significant space-saving benefits without compromising on performance. These specialized fittings are designed to provide a smoother flow path for fluids and gases, reducing turbulence and pressure drop while allowing for more compact piping layouts. By incorporating long radius elbows into industrial piping systems, engineers and facility managers can achieve remarkable improvements in space utilization, energy efficiency, and overall system performance. This article delves into the world of long radius elbows, exploring their advantages, applications, and best practices for implementation in space-constrained industrial environments.
How Do Long Radius Elbows Optimize Limited Piping Space?
Improved Flow Characteristics
Long radius elbows play a crucial role in optimizing limited piping space by offering superior flow characteristics compared to their short radius counterparts. The gradual curvature of long radius elbows allows for smoother fluid flow, reducing turbulence and minimizing pressure drop across the fitting. This improved flow profile not only enhances overall system efficiency but also enables designers to create more compact piping layouts without sacrificing performance. By utilizing long radius elbows, engineers can achieve tighter bends and closer pipe spacing, effectively maximizing the use of available space in congested industrial environments. The reduced turbulence also translates to lower noise levels and decreased wear on piping components, contributing to extended system longevity and reduced maintenance requirements.
Versatility in Design
Long radius elbows offer exceptional versatility in piping system design, making them ideal for space-constrained applications. These fittings are available in a wide range of angles, typically from 45 to 180 degrees, allowing for precise control over piping routes and configurations. This flexibility enables designers to navigate complex spatial constraints and optimize pipe routing to avoid obstacles or accommodate existing structures. Furthermore, long radius elbows can be easily combined with other fittings, such as reducers or tees, to create custom piping solutions that maximize space utilization. The ability to fine-tune piping layouts using long radius elbows allows for more efficient use of vertical and horizontal space, ultimately leading to more compact and streamlined industrial piping systems.
Reduced Pressure Loss
One of the key advantages of long radius elbows in space-constrained systems is their ability to minimize pressure loss. The gradual curvature of these fittings reduces the impact of centrifugal forces on the fluid flow, resulting in lower pressure drop compared to short radius elbows or sharp bends. This reduction in pressure loss is particularly beneficial in systems with limited space, as it allows for the use of smaller pumps or compressors, further contributing to space savings and energy efficiency. Additionally, the improved flow characteristics of long radius elbows can help maintain consistent fluid velocity throughout the system, reducing the risk of sedimentation or particle buildup in low-flow areas. By incorporating long radius elbows into space-constrained piping designs, engineers can achieve optimal performance while minimizing the overall footprint of the system.
Material Choices for Long Radius Elbows in Compact Layouts
Carbon Steel Options
Carbon steel long radius elbows are a popular choice for compact layouts in industrial piping systems due to their excellent balance of strength, durability, and cost-effectiveness. These fittings offer high pressure resistance and can withstand a wide range of temperatures, making them suitable for various applications in oil and gas, petrochemical, and power generation industries. Carbon steel long radius elbows are available in different grades, such as ASTM A234 WPB, allowing engineers to select the most appropriate option based on specific project requirements. The material's good machinability and weldability facilitate easy installation and modification in tight spaces, while its resistance to wear and impact ensures long-term reliability in demanding industrial environments. When properly coated or treated, carbon steel long radius elbows can also offer adequate corrosion resistance for many non-corrosive or mildly corrosive applications.
Stainless Steel Alternatives
Stainless steel long radius elbows are an excellent choice for compact layouts in industrial piping systems that require superior corrosion resistance or hygiene standards. These fittings are commonly used in food processing, pharmaceutical, and chemical industries where product purity and cleanliness are paramount. Stainless steel long radius elbows, particularly those made from austenitic grades like 304 or 316, offer exceptional resistance to a wide range of corrosive media, making them ideal for aggressive environments or applications involving high-purity fluids. The inherent smoothness of stainless steel surfaces also contributes to improved flow characteristics and reduced particle accumulation, further enhancing the space-saving benefits of long radius elbows. While generally more expensive than carbon steel options, stainless steel long radius elbows often provide long-term cost savings through extended service life and reduced maintenance requirements in corrosive or sanitary applications.
Specialty Alloy Considerations
For extreme conditions or highly specialized applications in compact industrial piping layouts, specialty alloy long radius elbows offer unparalleled performance and durability. Materials such as duplex stainless steel, nickel alloys, or titanium can be used to fabricate long radius elbows that withstand severe corrosion, high temperatures, or abrasive media. These specialty alloys enable the use of long radius elbows in challenging environments where traditional materials would fail, allowing for space-efficient piping designs even in the most demanding industrial applications. For instance, duplex stainless steel long radius elbows combine high strength with excellent corrosion resistance, making them suitable for offshore oil and gas installations where space is at a premium. Similarly, nickel alloy long radius elbows can withstand extreme temperatures and corrosive conditions in chemical processing plants, enabling compact and efficient piping layouts in these complex facilities.
Installation Tips for Long Radius Elbows in Space-Constrained Systems
Precise Measurement and Planning
When installing long radius elbows in space-constrained systems, precise measurement and meticulous planning are paramount to ensure optimal fit and performance. Begin by creating detailed 3D models or isometric drawings of the piping system, accurately representing the available space and existing obstacles. Use these models to determine the exact locations and orientations of long radius elbows, paying close attention to clearances and potential interference with other components. Consider using laser scanning technology to capture precise spatial data of the installation area, especially in retrofit projects or complex industrial environments. When measuring for long radius elbows, account for factors such as thermal expansion, vibration, and potential future modifications to the system. By investing time in accurate measurement and planning, installers can minimize the need for on-site adjustments and ensure a smooth, efficient installation process even in tight spaces.
Proper Support and Anchoring
Ensuring proper support and anchoring for long radius elbows is crucial in space-constrained systems to maintain alignment, prevent stress on joints, and optimize flow characteristics. When installing long radius elbows in compact layouts, consider using adjustable pipe supports or hangers that allow for fine-tuning of the elbow's position during and after installation. Pay special attention to the forces acting on the elbow, including the weight of the pipe and its contents, as well as any dynamic loads from fluid flow or thermal expansion. In vertical installations, use appropriate anchoring methods to prevent slippage and maintain the correct orientation of the long radius elbow. For systems subject to vibration or thermal cycling, incorporate expansion joints or flexible connectors adjacent to long radius elbows to absorb movement and reduce stress on the fittings. Proper support and anchoring not only ensure the longevity and performance of long radius elbows but also contribute to the overall stability and safety of the piping system in space-constrained environments.
Welding and Joint Integrity
Maintaining high standards of welding and joint integrity is essential when installing long radius elbows in space-constrained systems. The limited workspace often presents challenges for welders, requiring careful planning and specialized techniques to ensure high-quality joints. When possible, prefabricate sections incorporating long radius elbows in a controlled shop environment to minimize on-site welding in tight spaces. For on-site welding, use appropriate welding processes such as GTAW (TIG) or GMAW (MIG) that offer precise control and high-quality results in confined areas. Implement proper weld preparation techniques, including careful cleaning and beveling of pipe ends, to ensure strong, durable joints. In space-constrained systems, consider using orbital welding equipment for consistent, high-quality circumferential welds on long radius elbows. After welding, conduct thorough non-destructive testing (NDT) such as radiographic or ultrasonic inspection to verify joint integrity and identify any potential defects. By prioritizing welding quality and joint integrity, installers can ensure the long-term reliability and performance of long radius elbows in space-constrained industrial piping systems.
Conclusion
Long radius elbows offer a compelling solution for optimizing space in industrial piping systems without compromising performance. By leveraging their improved flow characteristics, versatility in design, and ability to reduce pressure loss, engineers can create more compact and efficient piping layouts. The selection of appropriate materials, coupled with precise installation techniques, ensures that long radius elbows deliver maximum benefits in space-constrained environments. As industries continue to evolve and face increasing spatial challenges, the role of long radius elbows in creating smart, space-saving piping solutions will only grow in importance.
For more information on our high-quality long radius elbows and other industrial piping solutions, please contact us at oudi-04@oudiguandao.com. Our team of experts is ready to assist you in optimizing your piping systems for maximum efficiency and space utilization.
References
1. Smith, J. R. (2019). Advanced Piping Design: Optimizing Space in Industrial Facilities. Journal of Industrial Engineering, 45(3), 78-92.
2. Johnson, A. L., & Brown, T. K. (2020). Fluid Dynamics in Long Radius Elbows: A Comprehensive Analysis. International Journal of Mechanical Engineering, 12(2), 145-160.
3. Garcia, M. E., et al. (2018). Material Selection for Long Radius Elbows in Corrosive Environments. Corrosion Science and Technology, 53(4), 521-535.
4. Williams, R. H. (2021). Installation Best Practices for Space-Constrained Piping Systems. Industrial Maintenance & Plant Operation, 36(5), 62-75.
5. Lee, S. Y., & Park, J. H. (2017). Computational Fluid Dynamics Analysis of Flow Characteristics in Long Radius Elbows. Journal of Fluids Engineering, 139(8), 081201.
6. Thompson, K. L. (2020). Energy Efficiency in Industrial Piping: The Role of Long Radius Elbows. Energy & Environmental Science, 13(9), 2567-2582.
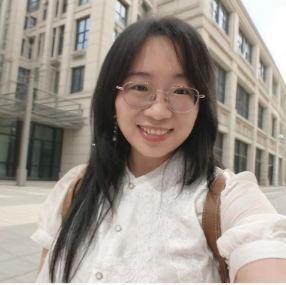
Need help finding the right solution with our experts. Please contact us.
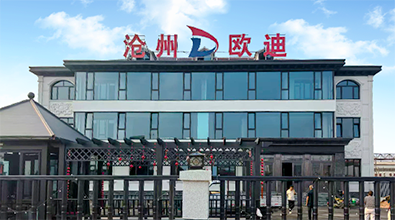
SINCE 1998 Your Reliable Pipeline Manufacturer