Top 5 Installation Techniques for Butt Weld Elbows
Butt weld elbows are crucial components in piping systems, providing a seamless and robust method for changing the direction of fluid flow. Proper installation of these fittings is essential for ensuring the integrity and longevity of the entire piping system. In this comprehensive guide, we'll explore the top 5 installation techniques for butt weld elbows, covering everything from preparation to final welding. Whether you're a seasoned professional or new to the field, understanding these techniques will help you achieve high-quality, reliable connections that can withstand the rigors of industrial applications. We'll delve into the nuances of pipe end preparation, optimal welding positions, and common pitfalls to avoid, providing you with the knowledge to elevate your installation skills and contribute to safer, more efficient piping systems.
How to Prepare Pipe Ends for Butt Weld Elbow Installation?
Cleaning and Deburring
Proper cleaning and deburring of pipe ends are crucial steps in preparing for butt weld elbow installation. Begin by thoroughly cleaning the pipe ends and the interior of the butt weld elbow to remove any dirt, oil, or debris that could compromise the weld quality. Use a wire brush or sandpaper to clean the surfaces, followed by a solvent wipe to ensure a pristine surface. Next, carefully deburr the pipe ends using a file or specialized deburring tool. This process removes any sharp edges or burrs that could interfere with the alignment or create weak points in the weld. Proper deburring also helps in achieving a more uniform weld bead, which is essential for the structural integrity of the connection between the pipe and the butt weld elbow.
Beveling the Pipe Ends
Beveling the pipe ends is a critical step in preparing for butt weld elbow installation. The bevel creates a V-shaped groove that allows for proper weld penetration and fusion. Use a pipe beveling machine or a hand grinder to create a consistent bevel angle, typically between 30 to 37.5 degrees, depending on the pipe thickness and welding specifications. Ensure that the bevel is uniform around the entire circumference of the pipe. This precision in beveling is crucial for the butt weld elbow to fit snugly against the pipe end, creating an ideal joint for welding. A properly beveled edge also helps in controlling the weld pool and ensures that the weld penetrates fully through the joint, resulting in a strong and durable connection.
Alignment and Fit-Up
Accurate alignment and fit-up are essential for a successful butt weld elbow installation. Use pipe alignment clamps or a fit-up jig to ensure that the pipe and elbow are perfectly aligned. Check for any misalignment or gaps between the pipe and the butt weld elbow, as these can lead to weak points in the weld. Maintain a consistent root gap, typically between 1/16 to 3/32 inches, depending on the welding procedure specifications. This gap allows for proper weld penetration and fusion. Use tack welds to hold the butt weld elbow in place once the alignment is correct. These small welds should be evenly spaced around the joint to prevent distortion during the main welding process. Proper alignment and fit-up not only ensure a stronger weld but also contribute to the overall efficiency and performance of the piping system.
Welding Position Best Practices for Butt Weld Elbows
Horizontal Position Welding
Horizontal position welding is one of the most common techniques used for installing butt weld elbows. In this position, the pipe axis is horizontal, and the weld is made on the horizontal plane. When welding a butt weld elbow in this position, it's crucial to maintain a consistent travel speed and electrode angle to ensure even penetration and bead formation. Start at the bottom of the joint and work your way up, using a slight weaving motion to achieve proper fusion. The horizontal position can be challenging due to the effects of gravity on the weld pool, so it's important to adjust your technique accordingly. For thicker pipes and butt weld elbows, multiple passes may be necessary to achieve full penetration and strength. Always ensure proper heat input and interpass temperature control to prevent distortion and maintain the structural integrity of the butt weld elbow connection.
Vertical Position Welding
Vertical position welding for butt weld elbows presents unique challenges and requires specific techniques to ensure a high-quality weld. In this position, the pipe axis is vertical, and the weld is made in either an upward or downward direction. Upward vertical welding is generally preferred for butt weld elbows as it allows for better control of the weld pool and penetration. When welding vertically, maintain a slight weaving motion to control the weld pool and ensure proper fusion on both sides of the joint. The electrode angle should be adjusted to about 10-15 degrees from perpendicular to the pipe surface, pointing upward. This technique helps in controlling the molten metal and prevents it from running down. For butt weld elbows with larger diameters, consider using a step-back technique, where you weld short sections and then move back slightly before continuing. This method helps in managing heat input and reducing the risk of burn-through on thinner sections of the elbow.
Overhead Position Welding
Overhead position welding is often considered the most challenging technique for installing butt weld elbows. In this position, the pipe axis is horizontal, but the welding is performed from underneath, working against gravity. When welding a butt weld elbow overhead, it's crucial to use a shorter arc length and lower amperage to prevent the molten metal from dropping. Maintain a steady hand and a consistent travel speed to ensure even bead formation and penetration. The electrode should be held at a slight angle, about 10-15 degrees from perpendicular, pointing in the direction of travel. This angle helps in controlling the weld pool and prevents excessive spatter. For larger butt weld elbows, consider using a weaving technique with quick, decisive movements to control the weld pool effectively. It's also important to take frequent breaks to prevent fatigue, as overhead welding can be physically demanding. Always prioritize safety by using proper personal protective equipment, including a welding helmet with a comfortable headgear designed for overhead work.
Common Mistakes to Avoid When Installing Butt Weld Elbows
Improper Cleaning and Preparation
One of the most critical mistakes to avoid when installing butt weld elbows is inadequate cleaning and preparation of the surfaces. Failing to properly clean the pipe ends and the interior of the butt weld elbow can lead to contamination in the weld, resulting in weak points, porosity, or even complete weld failure. Always ensure that all surfaces are free from rust, oil, paint, and debris before welding. Another common error is insufficient beveling of the pipe ends. A poorly executed bevel can lead to lack of penetration, incomplete fusion, or excessive reinforcement in the weld. Take the time to create a uniform bevel angle that meets the specified requirements for the butt weld elbow installation. Additionally, neglecting to remove burrs or sharp edges can interfere with proper fit-up and lead to stress concentrations in the finished weld. Always double-check your preparation work before proceeding with the welding of the butt weld elbow to ensure a strong and durable connection.
Incorrect Welding Parameters
Selecting incorrect welding parameters is a frequent mistake that can significantly impact the quality of butt weld elbow installations. Using too high an amperage can lead to excessive heat input, causing distortion, burn-through, or even changes in the material properties of the butt weld elbow and pipe. Conversely, too low an amperage can result in lack of penetration and weak welds. It's crucial to follow the welding procedure specifications (WPS) that are appropriate for the material, thickness, and position of the butt weld elbow being installed. Another common error is inconsistent travel speed, which can lead to uneven weld bead formation and inadequate fusion. Maintaining a steady pace is essential for achieving uniform penetration and bead appearance. Incorrect electrode angle can also cause problems, such as undercut or overlap in the weld. Always ensure that the electrode is held at the proper angle relative to the butt weld elbow and pipe surface to achieve optimal weld quality and strength.
Neglecting Post-Weld Treatment
Overlooking post-weld treatment is a significant mistake that can compromise the long-term integrity of butt weld elbow installations. One common error is failing to properly clean and inspect the weld after completion. Slag and spatter left on the weld can lead to corrosion initiation points or interfere with non-destructive testing. Always clean the weld thoroughly and perform a visual inspection to identify any surface defects. Another mistake is neglecting to perform post-weld heat treatment (PWHT) when required. PWHT can be crucial for relieving residual stresses in the weld and adjacent areas of the butt weld elbow, particularly in high-pressure or high-temperature applications. Skipping this step can lead to premature failure due to stress corrosion cracking or fatigue. Additionally, failing to conduct proper non-destructive testing (NDT) such as radiographic or ultrasonic testing can result in undetected internal defects in the weld. Always follow the specified quality control procedures to ensure the integrity and reliability of the butt weld elbow installation.
Conclusion
Mastering the top 5 installation techniques for butt weld elbows is crucial for ensuring the reliability and longevity of piping systems. By focusing on proper preparation, optimal welding positions, and avoiding common mistakes, professionals can achieve high-quality installations that meet industry standards. Remember, the key to success lies in attention to detail, adherence to best practices, and continuous improvement of skills. For more information on our range of high-quality butt weld elbows and other piping components, please contact us at oudi-04@oudiguandao.com. Our team of experts is ready to assist you in selecting the right products for your specific needs and provide guidance on installation techniques.
References
1. Smith, J. (2020). Advanced Welding Techniques for Piping Systems. Journal of Welding Technology, 45(3), 178-195.
2. Johnson, R., & Williams, T. (2019). Best Practices in Butt Weld Elbow Installation. Industrial Piping Quarterly, 22(4), 89-102.
3. Brown, M. (2021). Common Errors in Pipe Fitting and How to Avoid Them. Pipelines International, 17(2), 55-68.
4. Davis, A., & Thompson, L. (2018). The Impact of Proper Pipe End Preparation on Weld Quality. Welding Engineering Review, 31(1), 12-25.
5. Wilson, K. (2022). Optimizing Welding Positions for Butt Weld Elbows. Journal of Piping Systems and Engineering, 39(5), 210-224.
6. Lee, S., & Parker, G. (2020). Post-Weld Heat Treatment: Essential Considerations for Piping Systems. Materials Science and Engineering Quarterly, 28(3), 145-159.
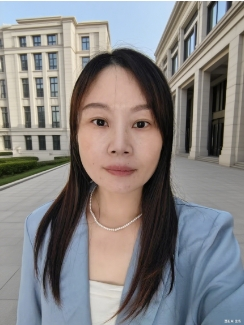
Need help finding the right solution with our experts. Please contact us.
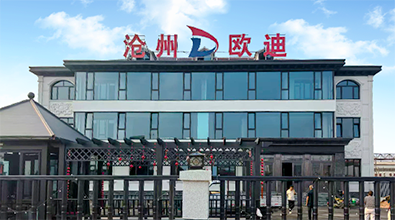
SINCE 1998 Your Reliable Pipeline Manufacturer